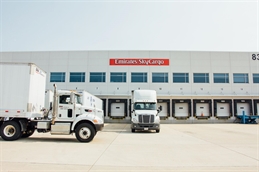
Worldwide Flight Services (WFS) took its handling capabilities for pharmaceuticals at Copenhagen airport to a new level this month with the opening of a state-of-the-art building dedicated to this cargo.
Built to handle up to 300 euro-pallets, the company’s 1,500 sqm terminal caters to pharma products that require constant temperature in a range of 2-8°C or 15-25°C. It is designed for end-to-end handling in a temperature-controlled environment from acceptance, offload and pre-storage to build-up and storage for loose shipments and prebuilt pallets.
Morten Mortensen, the airport’s director of airline sales and route development, said that the handler has set a new standard for the handling of pharmaceutical products at Copenhagen.
Another dedicated pharma terminal under the WFS banner opened at Paris Charles De Gaulle airport this month. The €10 million (US$ 11.14 million) building is the only dedicated pharma facility at CDG that is owned by a ground handler.
“WFS has a vital role to play in helping our customers deliver the quality of service they have promised and in ensuring we consistently perform to the high standards required for sensitive, temperature-controlled cargoes to protect their integrity throughout the cool chain,” said Hugo Rodrigues, the handler’s vice president for cargo, France. “At a major air cargo gateway like Paris CDG, we believe it is incumbent on ground handlers to invest in the right equipment to handle pharma products.”
The 2,400 sq m building has multiple rooms for different temperature ranges and is equipped with a new warehouse management system that supports the use of barcode scanning for real-time storage capacity monitoring and management to allow constant tracking of shipments. Real-time temperature and humidity readings from the facility’s sensors are fed to a cloud platform that can be accessed from mobile devices.
Transfers to and from the ramp are handled by exclusively designed temperature-controlled three-pallet trailers and cool dollies.
WFS has opened pharma facilities in Johannesburg and Miami and is looking to set up another in Madrid.
Dedicated pharma facilities are on the rise. Earlier this year Emirates SkyCargo commenced handling pharma traffic in a 1,000 sq m building at Chicago O’Hare airport developed in partnership with ground handling firm Maestro. It can process 15,000 tonnes of pharmaceuticals a year.
Forwarders are also investing in pharma terminals. Last year GEFCO opened a dedicated pharma handling facility with a footprint of 15,000 sq ft near London Heathrow airport, the company’s third such temperature-controlled warehouse in Europe serving the life sciences and healthcare sector. Last December Kuehne + Nagel opened the largest pharma and healthcare warehouse in Slovenia for the global distribution of finished products and storage and distribution of production materials for the pharmaceutical industry.
In part, this trend reflects the ongoing growth of pharmaceutical traffic. The Business Research company projects the global pharma market to grow from US$934.8 billion in 2017 to US$1.17 trillion in 2021, a rise of 25.1%.
At the same time, requirements – both in terms of regulatory obligations and customer demands – are pushing up the bar. One handling executive predicts that the trend is going towards having a seamless operation, as regulatory pressure continues to build up.
For handlers this means significant investment. On top of the money spent on cooling infrastructure located on prime airport property, they have to invest in additional technology like IoT beacons for real-time monitoring.
Robert Fordree, executive vice president cargo at Menzies Aviation, said that the effort goes beyond the installation of technology to changing a company’s culture, and training plays a huge role in this.
In addition to devouring time and money, pharma facilities also have repercussions on productivity. A cooler takes up space that cannot be used for other commodities. Hence traffic has to generate sufficient volume to justify the investment versus a more flexible approach to space to handle a mix of commodities.
This limits the choice of stations where dedicated pharma facilities are viable.
“No handler is going to build a dedicated pharma facility in every market,” said Fordree. He sees the concept limited to certain hubs, where they are built on the basis of airline and forwarder expectations.
According to Dan Parker, senior vice president commercial cargo – EMEAA at WFS, his company’s focus is very much driven by customer needs and underlying market conditions.
“We see significant potential in Copenhagen by investing in the facilities and solutions our customers need to grow their business. Pharma is a big focus because both Denmark and Sweden have important pharmaceutical production sites located in or around the Oresund region and Copenhagen is a natural international gateway for these products,” he remarked at the opening of the new WFS facility in Scandinavia.
Likewise, certification of facilities and processes is driven in the main by customer requirements. Menzies is in the process of obtaining CEIV accreditation in Amsterdam and management is looking at going down the same route in London, Sydney and Melbourne.
For the most part, this should not require much beyond the time and effort spent on going through the certification process itself. “We always work towards the principles of standards like CEIV or GDP, even where we don’t have the certification,” said Fordree.
By Ian Putzger
Air Freight Correspondent | Toronto
