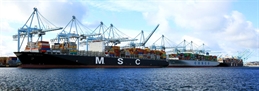
California seaports are arriving at their new normal. Ships are now able to come into dock at San Pedro Bay’s Ports of Los Angeles and Long Beach in Southern California, and vessel backlogs have cleared at San Francisco Bay’s Port of Oakland in Northern California.
“At peak there were more than 30 cargo ships at anchor in San Pedro Bay,” comments Phillip Sanfield, Port of Los Angeles spokesman. “But it began to clear after February 20.”
In March, cargo volumes were up 23% for both San Pedro Bay ports. In April, cargo volumes at the Port of Long Beach were up another 7.9%. But with vessel schedules not totally back in sync, the Port of Los Angeles reported a 6.1% decline in April.
“The port had predicted the backlog to clear by late May, but by May 1st the anchorage issue dissolved,” Sanfield says. “In fact, several times in May, three 13,000-TEU ships were docked concurrently at Pier 400 at the Port of Los Angeles.”
The Port of Oakland saw cargo increase 6.4% over March 2014 figures, which resulted in a turnaround from a 31% decrease in January and February. Containerized cargo volume increased again in April by 1.7% over April 2014 figures.
“Labour productivity has been restored and transaction times at marine terminals have improved,” says Mike Zampa, Port of Oakland spokesman.
Ports of Los Angeles and Long Beach executives recognize that while stabilization at the seaports is largely based on the new labour contract recently ratified by West Coast dockworkers and employers, both ports still face other congestion-related challenges, such as the logistical problems of processing supersized ships in a timely manner.
Port of Long Beach CEO Jon Slangerup emphasizes that “settling for returning to normal” is not good enough. “We need a new normal where the port facilitates faster, more reliable and lower cost shipping through here,” he says.
Consequently, in an unprecedented step, the rival seaports are working together to “optimize” the supply chain. A formal discussion agreement was approved by the Federal Maritime Commission (FMC) that allows both ports to discuss how to cooperate, work with stakeholders from throughout the supply chain and communicate the results of the efforts. This means the two ports can cooperate far more strategically on finding new ways to prevent congestion and cargo delays, improve the transportation network, and enhance environmental sustainability and security.
“Essentially, the ports can now talk about everything – except price and terms,” Sanfield explains. “Both ports will still compete, and there’s no plan to merge.”
A series of meeting have been held in recent weeks to discuss all issues. In mid-April, more than 100 cargo owners, trucking firm leaders, longshore labour, marine terminals and other goods-movement industry representatives turned out for a joint meeting hosted by the ports to gather input, insights and solutions focused on improving the performance of the supply chain.
“Now we’re forming seven working groups to focus on improvements in peak season 2015, container terminal optimization, chassis ops, off-dock solutions, key performance indicators/data solutions, intermodal rail and drayage,” reports Art Wong, Port of Long Beach spokesman. “Working with us will be our key stakeholders: shipping lines, cargo owners, labour, railroads, trucking interests, equipment owners and more.”
Meeting in early June, the peak season 2015 working group was the first to meet. Their job is to drill down on this year’s peak demand needs.
In addition to the supply chain optimization initiatives, both ports are looking at short and long term solutions to increase efficiency and improve reliability.
On February 25, the Port of Los Angeles implemented a “peel off” programme to streamline container moves. Here the port teamed with The Pasha Group stevedoring company, harbour trucking firm Total Transportation Services Inc (TTSI), several marine container terminal operators and a core group of major retailers to create the programme that involves “peeling off” containers of high-volume customers to a near-dock yard about three kilometres away where they are sorted for destination to inland distribution centres.
Under peel off, import containers loaded with goods belonging to high-volume shippers are stacked together in a block upon arrival at the Port. The terminals expedite TTSI trucks through their gates to retrieve the containers and deliver them to the near-dock yard where they are sorted. The same trucks loop back to the terminals for the next inbound container. The trucks keep boxes moving by delivering outbound containers on the return leg.
According to Sanfield, the trucks make five to six turns a day. Cargo owners can move their containers through the peel off yard in less than 48 hours and make those trips at night during off-peak traffic hours. TTSI has leased 250 chassis to ensure containers are on wheels and ready to roll.
The yard is open six days a week from 7 a.m. to 3 a.m. Nearly seven hectares are available for staging up to 500 containers. As demand grows, the facility can operate 24/7 and accommodate up to 650 containers.
International Longshore and Warehouse Union (ILWU) workers handle all gate and terminal operations at the peel off yard, including on-site chassis inspection, maintenance and repair.
In addition, on March 1, the Ports of Los Angeles began working with chassis operators to develop an interoperable chassis pool.The programme is open to all container terminals and may be expanded to other locations in the harbour complex.
“By April 21, 1 million chassis moves were made, which represented a 30% increase in operations efficiency compared to pre-pool operations,” Sanfield says.
The Port of Long Beach is replicating the programme.
Technology is another area in which the Port of Los Angeles is working to build increased efficiencies. On June 3, the port announced that Cargomatic, a privately-owned technology company that matches trucking capacity with shipments, is testing its mobile app for speeding up the flow of containerized cargo.
The company has developed a peel-off like concept it calls the “Cargomatic Free Flow” programme that offers a web-based solution to optimize container moves for cargo owners, terminals and trucking companies. Port officials report that preliminary results are encouraging.
Sanfield describes the new technology as “basically Uber software for trucking companies” to speed truck times at gates. “We are actively engaged at looking at new technologies that will help truckers get in and out of gates,” he says.
Cargomatic’s goal is to move at least 1,000 containers a week through the port.
Meanwhile, the Port of Long Beach continues to invest in terminal improvements. Wong reports that construction of the 69-hectare first phase of the port’s Middle Harbor modernization project will be complete this summer.
“It will be the most advanced, automated terminal in North America and will be the world’s greenest terminal with nearly all-electric and nearly zero emissions,” he says.
When competed in early 2016, the project is expected to increase port capacity by 10% and be capable of working two 18,000-TEU vessels at a time. “With the second phase, opening late in 2019, Middle Harbor will be able to accommodate 21,000-TEU vessels,” Wong adds.
In addition, three other terminals at the Port of Long Beach are raising their cranes and/or taking delivery on new, taller cranes within the next couple of years so they can handle much larger ships up to 16,000 TEUs.
In Northern California, the Port of Oakland has announced a four-step programme to improve cargo movement. Elements of the programme include: Saturday operations every week to alleviate weekday crowding inside terminals; locations outside terminals where cargo could be dropped off or picked up after hours; electronic monitoring to measure wait-times at terminal gates, and a “grey” chassis fleet that permits harbour truckers to use any chassis at any terminal to haul cargo over the road.
In late March/early April, the port experienced a cargo glut as a result of vessels reaching Oakland off-schedule and in bunches after delays at congested Southern California ports. Harbour truckers reported that, in some instances, they waited two hours or more to pick up containers.
The port’s cargo-acceleration programme is intended to address slowdowns and long waits. Regular Saturday gates would spread cargo pickup and delivery over an extra day each week, relieving stress on terminal operations. Offsite locations would enable truckers to transact business without entering terminals. Monitoring would provide drivers with up-to-the-minute wait times so they could avoid peak periods of activity. The grey chassis pool should minimize periodic shortages of chassis that delay cargo delivery.
Already by mid-April, port officials reported that the backlog of ships awaiting berths had been cleared and that vessel schedules were normalizing. On May 13, the port reported that 16 big ships had called at Oakland in the past 30 days, indicating that Oakland is “fully engaged with the mega-ships that are changing the face of global trade.”
Faster cargo movement is viewed as the last big hurdle in correcting marine terminal delays.
Unlike the Port of Oakland, the Port of San Francisco handles primarily break and bulk break cargoes, but it, too, was impacted by the backlog of ships anchored in San Francisco Bay. But Jim Maloney, Port of San Francisco maritime spokesman, explains that the backlog is clearing up.
“The port experienced a shortage of labour because of allocated labour based on when ships arrive in the bay,” he says.
The port’s bulk ships terminal operator has a separate contract agreement with the ILWU, which protected them. “They were able to get labour on a priority basis,” he explains.
Ninety percent of the port’s freight comes from Asia (South Korea, China, Japan, and Taiwan) with most break bulk shipments being steel. The port also imports large quantities of aggregate from British Columbia. Driving the business is a booming construction market between San Francisco and the Silicon Valley near San Jose.
Bulk cargoes drive most of the port’s business. There are plans, however, to develop Pier 96 into an export facility for iron ore and grain shipments to Taiwan, China, Japan and South Korea. Plans also call for using 28 hectares at Pier 80 for imported automobiles from Mexico. The port does not handle automobiles, but is close to signing a deal.
By Karen E Thuermer
Correspondent | Washington
